年賀状の制作 2024 [中] :版下作成〜調色作業 (1/2)
前回「企画からデザインまで」では、実際の印刷との兼ね合いを意識しつつの図案作成についてあれこれ書きました。本記事ではその後のできた図案を製版に起こしていく過程(プロセス設計〜版下作成)と、インクの調色(途中まで)について記述を続けます。やはり技術以外の余計な情報に溢れる内容となっておりますのでご容赦ください。
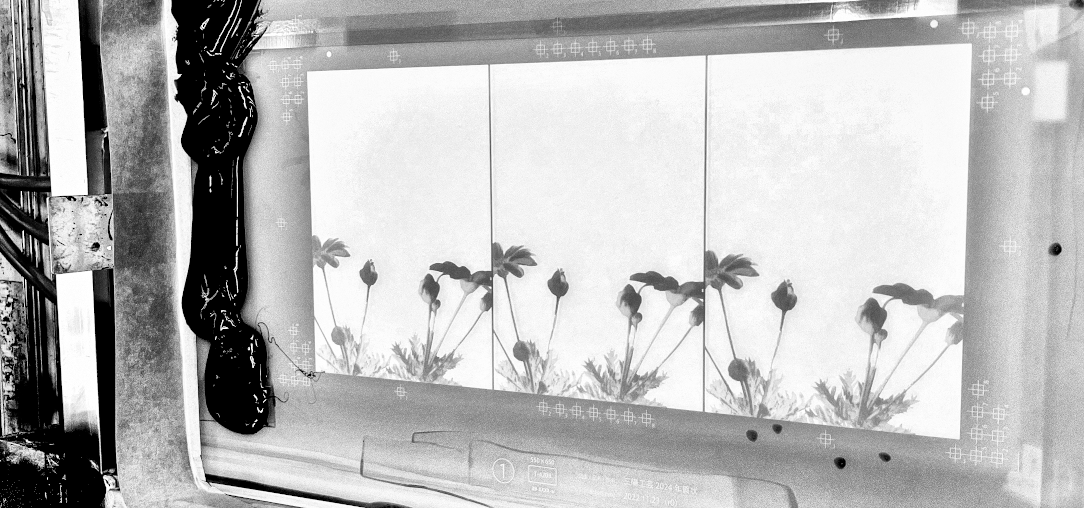
最初工程の刷り出しはいつも緊張する。ほろ苦い記憶。
C. 版下作成(プロセス設計)
C1. 印刷の実現性
デザイン作成過程の中でも何度か触れたように、当然ながら作り出したデザインが実際に印刷できなければ仕方がない。印刷「できる」という事だけ取れば、インクジェットでデータを丸っと、しらしらと出力すれば良い [*1]のであるが、ここで重要なのはシルクスクリーン印刷で「印刷できる」 ということである。なぜにシルクスクリーン印刷が重要か?という問いには、弊社は基本的にシルク印刷屋であって、 「刷り台がそこにあるから」と申せよう[*2]。
シルクスクリーン印刷(以後”シルク”と呼ぶ)はご存じのとおり、基本的には1版(1回の刷り)からは1つの色しか印刷できず、インクはいわば特色(CMYKなどの掛け合わせではなく、印刷する色そのものの色に調色したインク)を用いて行う。例えば信号機の絵を印刷する場合は、丸のパターンが製版された版で、1:緑色、2:黄色、3:赤色をそれぞれ印刷し(この信号機の場合は1〜3の順番はどれから良い)、最後に4:信号機の黒を長方形に丸が3箇所くり抜かれたパターンで印刷し出来上がり、というような要領である。各色を印刷するのは印刷の「工程」と呼ぶ。通常は複数工程を一度に印刷できず、1工程毎にインクを乾燥させてから、順番に次の工程に取り掛かる。印刷順序も重要で、先の信号機の例では、最初に鮮やかな色を印刷してから黒で印刷した。なぜそうしたかというと、黒の上に鮮やかな色を重ねて印刷するとインクの持つ隠蔽性の程度により、若干黒が透けることで彩度(鮮やかさ)が低下するのを避けるためで、さらに、赤/黄/緑の3つの丸は黒との重ねる位置が多少ずれても大丈夫なように、黒のくり抜かれた丸よりも少し大きめに印刷して(そのようにパターン=版下を作る)おく、 というような工夫[*3]をする。

印刷順序とトラッピングについて
それでは今回のデザインに対してはどうか、という話に移るのだが以下のように設計した。リストの下の画像は [右]シルクの版下データ(インクジェットの場合はプリントデータ)と[左]印刷イメージ(PCの画像)を並べた。尚、左の版下データの黒い部分が印刷されるところである。
1.【シルク1】透過アンバー:地色/デイジー [T420]
左のイメージで薄い色が紙の地が見えているところである。
![【シルク1】透過アンバー:地色/デイジー [T420]](
https://www.sanyoukougei.co.jp/technical/nenga2024/20245614467.png
)
2.【シルク2】パール:セル(鱗)の反射下地 [T200]
![【シルク2】パール:セル(鱗)の反射下地 [T200]](
https://www.sanyoukougei.co.jp/technical/nenga2024/202456144614.png
)
3.【IJP】CMYK:セル(鱗)のカラー、光彩、弊社ロゴマーク
インクジェットで透明色をプロセス2に重ねて、パールの反射に色を付ける狙いがある。

4.【シルク3】黒:目、斑点 [T420]
目の位置が合うだろうか(ここがズレるとタツの表情が変わるだろう)。
![【シルク3】黒:目、斑点 [T420]](
https://www.sanyoukougei.co.jp/technical/nenga2024/202456144629.png
)
5.【シルク4】オレンジ〜グリーンのグラデーション:網目の線描 [T330]
今回の肝になる工程と思われる。位置合わせも厳しい...。
![【シルク4】オレンジ〜グリーンのグラデーション:網目の線描 [T330]](
https://www.sanyoukougei.co.jp/technical/nenga2024/202456144636.png
)
6.【シルク5】透過ホワイト(薄い):陰影濃淡/プランクトン [T330]
ここもインクの透過率の設定などあり、うまくイメージ通りとなるかどうか。
![【シルク5】透過ホワイト(薄い):陰影濃淡/プランクトン [T330]](
https://www.sanyoukougei.co.jp/technical/nenga2024/202456144644.png
)
7.【シルク6】透過ホワイト(濃い):ハイライト [T330]
![【シルク6】過ホワイト(濃い):ハイライト [T330]](
https://www.sanyoukougei.co.jp/technical/nenga2024/202456144651.png
)
8.【シルク7】オーカー〜グリーンのグラデーション:海藻/メッセージ [T330]
またグラデーションだ。
![【シルク7】オーカー〜グリーンのグラデーション:海藻/メッセージ [T330]](
https://www.sanyoukougei.co.jp/technical/nenga2024/202456144658.png
)
9.【シルク8】赤:2024/Peace [T200]
![【シルク8】赤:2024/Peace [T200]](
https://www.sanyoukougei.co.jp/technical/nenga2024/20245614476.png
)
と、ここでは触れていないハガキの表面の印刷も合わせると合わせて10工程。工程が増えていくと、一つの部分においては色や質感の階調差が詰まる=階調がなだらかに/より繊細になっていくが、複数に分散された各部分に対しては10工程程度ではそれぞれそれなりに見せるという程度だけども、普段の仕事と比べると大分工程が多い。このプロセスでの版下データを作成する。リスト中の[]内の数値はシルク版のメッシュ数[*4]である。細かいパターンが多いので全体にハイ(網目の密度が高い)メッシュ寄りだが、パールなどの顔料/フィラー粒径の大きいインクでの印刷にはT200を用いる。プロセス3にはインクジェット(IJP)での印刷を入れている。これは単純に色数と光彩のグラデーション表現のためで、こちらで表明した通りこの色数とグラデーションの密度はシルクでは難しい。弊社のロゴもIJPだが、これは(表現上)重要でない箇所にわざわざシルクの工程を増やしたくないから、ついでに印刷しておくのである。
先のデザインデータでは、実際の印刷工程を想定/シミュレーションする上で、工程毎にレイヤーに分けてデータを積んでいったので、基本的にレイヤーの並びは印刷工程順序に対応している。
ここで迷ってしまったのは、点と線の太さである。経験上、安定的に印刷できる最小パターンとしては、点でφ0.12、 線幅で0.1mm程度であるが[*5]、ここでデータ側のモニタ上の見栄えと実際の印刷結果の印象とでは異なることが問題になる。色にも似たことが言えるがデジタルのモニタ上での虚像と印刷物の実像との差[*6]は、最終的には結果として印刷された物(印刷物)を見た人の主観に依るので、印刷されてないデータの段階では、いわば経験と勘、またはフィジカルなサンプルなどを頼りにするしかない。工業製品などで図面指定があるものは、その通りにやれば良いが(その結果、見栄えのしないものが出来たとしても「え?、図面通りですけど?[*7]」と言えば良い)、今回は見た目が全てのイラストである。データ(モニタ)上はよく見えても実際に印刷すると細すぎたということは去年のうさぎのヒゲで経験していたので、版下の段階で気持ち太め(線幅0.1mmから0.16mm)に調整した(が、これが余計な作為であったのは後の印刷で明るみになる)。
シルクスクリーン印刷において、データと印刷物の違いと言う点では、もう一つ、透明色の描画についてモニタの問題とは異なる注意が必要である。例えばデザインデータ上で透明色のハッチング、点描などで描く時に、そのハッチングの線が重なると当然その重なり部分が濃く見えるが、これが立体感など表現上プラスの効果を持ってしまっているとする。この透明色のパートを一つの工程として印刷する場合、ハッチング部分は単なる2値的なパターンに変換されて「重なり」の情報は失われるので部分的な濃い薄いの効果は失われる。したがって元のデータよりも印刷物は平坦な印象になる可能性が高い。よって重要なパートがこのような重なりを持つデータの時は、デザイン製作の節目の段階で、印刷と同じく見える重なりのないデータに変換して確認した方が良い。単純なことなのだが、これをうっかり怠ると刷り上がりを見て落胆する可能性が高くなると思われる。

2023年のうさぎの例。半透明の線で描いたハッチング部分を版下データ化(2値化)した効果。ハッチング描画時にはあった明暗の幅が平坦な印象に...
版下はそれぞれの工程を3面付で作成した。弊社は製版を外部の製版会社へ委託しているので、製版用のデータをそちらへ送り、あとは製版のプロにお任せするより他ない。
*1:これは文脈上わかりやすい対比として書いたが、実際はむしろほとんど皮肉である。するりとデータ通りに出てくれれば苦労はなくて、そんなに簡単ではない。
*2:シルク印刷が多いですが、パッド印刷、インクジェット、関連加工も手掛けております(PR)。
ここでシルク印刷が重要であるという主張を繰り広げることも可能だが、当然ながらほかの印刷方式であってもそれぞれの技術/ノウハウを駆使することで、特徴のある印刷ができるので、ことらさシルクを持ち上げるような姿勢は慎む。というよりも自分でもシルクに拘る理由が理解できないが、自分の「手で刷る」感覚に馴染みがあるというだけの気もする。シルクの印刷機というのもありながら。
*3:この工夫(というか事実上ルーチンだが)は業界ではトラップ(トラッピング)と呼ぶようだ。(ようだ?実は弊社では「(パターンを)オフセットする」と呼んでいる)
*4:メッシュとはシルク版に張る紗のことである。メッシュ数は通常dipのように1インチ中に張られた糸の本数で表す。概ねとしてはメッシュ数が高くなるにつれ細かい図像を印刷できる反面、インクの吐出量が抑えられて(=塗膜が薄くなって)いく。大きめの粉体(顔料/フィラー)の配合されたインクを使用する場合はインク中に含まれる粉体をこの紗の隙間から通すため、顔料/フィラーサイズに対応したメッシュ数の選定を行う。アルファベットのTは紗の糸の素材(T=テトロン=ポリエステル)を指す。通常の工業製品の文字印刷などでは#270〜#300メッシュを用いることが多い。(メッシュと印刷結果の関係についてこの脚注では骨子の説明のみとしたが、実際にはメッシュのパラーメータだけでも他に:材質/線径(開口率)/織/テンション/その他特殊な処理...などあり、それぞれの違いにより印刷結果も異なる。また弊社のような工業製品への印刷の他に、電子基盤、アパレルなど同様なスクリーン印刷の技法が用いる業界があるが、原理は共通していても、個々のパラメーター、設定条件などは大分差がある)
*5:パターン(版のインクが出る開口部)の密度(集積状況)にもよるだろう。この最小部分を突き詰めている会社はこれらの半分程度は可能らしい。
*6:現に(今時ほとんど)コンピューター上でグラフィックが作成されて、それが印刷物になっているので意外に思う方もおられるかもしれない。ハードの精度は上がっているが最終的には人の感性での判断によることが多いのではないか?我々工業製品の印刷では、基本的に色はフィジカルな色見本調(DICやPANTONE等)を基点とするケースがあり、ある程度客観的/数量的な評価ができる業界ではあるが、ここでも印刷物が人の官能に影響する状況が多々あり定量的とはなかなか行かないことも多い。
*7:プロ意識に欠ける対応か?。しかし図面通りにやって上手くない結果になるのは業務の中でよくある話で、通常は「念の為の確認ですが…」と一応顧客/ユーザーには(特に設計者/デザイナーの気分を害さぬよう細心の注意を払いつつ)お伺いを立てる。
D. 調色について(1/2)
D1. シルク1、2(アンバーとパール)
インクの色を作ることを誰が呼んだか調色と呼ぶ。印刷工程的にアンバーとパールのシルク2工程の後はインクジェットになるので、まずこの日は調色を並行させながらこれら最初の2工程分を印刷してしまう算段で取り掛かった。
iPadに映し出されたデザイン画面を見ながら容器の中でインクを混ぜ合わせ、大体こんなもんかしらと言ったところで、実際の紙に本番と同じメッシュの調色用の版で印刷を行う。乾いていない容器の中のインクと印刷して乾燥させたインクの色は大きく変化するのだが、相対的な変化量を推測しながら、足りない色を足していき、また印刷/乾燥を繰り返す。

背景のアンバーを調色中(残業の友:bluetoothスピーカーと共に)
またこのアンバーは紙の質感、ディティールを活かすため薄い透過色としたので、インクの肉厚(塗膜厚み)の違いによっても色の濃淡が変化する。インクの肉厚の調整パラメーターは、溶剤の量、版のメッシュ、スキージの角度やエッジの状態、押し込む力加減などの事項がある。そして今回は花の陰影部分の網点をパターンに忠実に出すために、インクの粘度を一定範囲内に収める必要がある。 網点は小さいので[*1]、この調整が不十分であるとインクが版に詰まってしまって網点のグラデーションの階調飛びが生じる。インクの詰まりを防ぐという観点では溶剤でインク粘度を緩めて版を通りやすくする、というのは手っ取り早い方法だが、網点の場合、点を出すと同時に点を抜くというように、細かいネガポジのパターンの再現を実現しないといけない[*2]ので、 粘度を下げ過ぎるとインクが流動し過ぎて(あるいは紙に染みて滲んでしまうかも?)細かい抜き部分が潰れてしまう可能性がある。さらに透明色の特徴的な事象として、枚数の多い印刷であると最初の刷り出しから、最後の刷り終わりまでの時間に版上に乗ってスキージーでこねられているインク中の溶剤が揮発し続けることで、色成分比率の上昇と塗膜の肉厚が増えることで徐々に印刷の色が濃く変化して、結果最初と最後の印刷物の色が違う、という事故も発生する。 このような不安定要素を避けるために遅乾メジューム(メジュームは色成分のない透明なインク。遅乾とは乾きが遅い=溶剤揮発による粘度変化を抑える)やハーフトーンベース(メジュームよりもインクの流動性を抑えたインク)などを加えて調整する。今回はさらに高精細な印刷用のインクとしてKSタイプの800メジュームインクをベースとした。[*3]
色合わせはモニターとの比較なので、畢竟自分の主観に頼らざるを得ない。とある時点でこの辺りが正解か、と見切りをつけて本番の印刷を開始した。ところが刷り進めていくうちに色味や濃淡の具合が徐々に心もとなく感じてくる。心もとなさの要因は、アンバーは濃い目の方が花の陰影がはっきりして良いのだが、あまり暗くなっても年賀状として辛く、そうかといって明る過ぎても花が見えてこないという、モニタと実物の色合わせの問題というよりも、年賀状はどうあるべきか、どこまでが年賀状として許されるのか、という社会的規範を巡って悩んでいたというのが正しい。その規範の範疇に入ると思える濃度に行き着くまで、3度程、色相を変えたり、彩度をあげたり、濃淡を直しながら印刷を進めた。本番の印刷をしながらなので、必然この間印刷したものは年賀状として各位へ送られていくのであるが、届くのはそれぞれ各1枚で、各位諸氏同士で見比べることもされないだろうから、黙っておけば大丈夫と踏んだ[*4]。

白ケント紙に印刷して、パターン再現状態を確認
紙の印刷面の凹凸には思った以上に影響されている。まず印圧を通常より必要とされていて、気を抜くと紙の凹部にインクが入らない。また凹んだ部分にはインクが少し厚く乗るので色が濃く出て、紙の質感を強調する。印圧をかけ過ぎたのか、花の陰影の階調が少し飛び気味になっているようだ。比較にケント紙に印刷してみたら、インクの詰まりや潰れはなく出ていて、印刷再現性としては問題ないようだ。あるいは紙の色でハイライトのレンジが抑えられたことによる印象かもしれない。
スキージーを持つ手に力を込めて印刷するが、スキージーの先端が圧力で寝てしまうので、 スキージーを立てる[*5]。手首の力と指先から手のひらの感覚、体の重心移動によって力加減のバランスを保ち、圧力と速度を安定させてスキージングを行う。版越しに指先に伝わる紙の凹凸の感触から適切な印圧を想像しつつ、一枚づつ印刷していく。などと書き綴るとなかなかの職人技のようである。が、毎日何百何千回、それを何年何十年も同じような行為を続けていれば大概の人はこの程度のことは自然とできるようになるので、このような身体運動ができたとしてもそんなことは自慢にならないし、自慢をしてみても良いが、要点が伝わらず反応は薄いと見る。
次の工程のパール層はパール顔料を混ぜる以外に色味などの味付けは不要であるので適当な配合比 [*6]でインクを調合すれば良い。パール顔料も複数種類があり、シルバー(これもたくさん種類がある)などのメタリック系のインクもいくつか交えてテスト印刷を行い、効果、雰囲気を確認した結果、結局当初から想定していたパールを採用した。
そして印刷を開始したのだが、前の工程の乾燥をさせ過ぎたためか、紙の伸縮、反りがすごい。工場内は静電対策で一定の湿度を 維持するよう加湿しているのだが、乾燥炉内とは当然湿度のギャップがあり、そのためか、乾燥から取り出して重ねて置いておくと、外気に当たる面から吸湿するのか、かなり反ってしまった。パールの版と合わせて見るのだが、紙の方が縮んで小さく、しかもその縮み方が均一ではなく、2辺の片側とその反対側では縮み方が異なっている。止む無く再度ドライラックに並べ直して、時間を置いて状態を見ることにした。
しばらくして、大分反りが治ってきたように見えたので、改めてパール版と重ねてみたが、多少元には戻ったものの、やはりピッタリには合わない。パールは以後に重ねる工程の全てに位置的に関わる工程なので、このパールを以降の位置合わせ基点とすることにして、印刷に取り掛かることにした。普段の業務でも樹脂フィルムの印刷はやはり同様の要因で伸び縮みがあるので、気を遣う。紙に対しても同様の認識は持っていたが、思った以上に扱いがデリケートだ。としらじらしく書くが、既にこの時、実は去年もは違えど同じ紙を使っていて、これと全く同じ経験をしていた事が記憶の底に残っていることにも気づいていた。
*1:最小点は0,1mmとした。余談であるが、AM変換で作るの網点の密度は線数で決まるのだが、点サイズの最小サイズが規定できない。よって弊社では点サイズが一定に設定できるFM変換を通常用いている。通常といっても工業製品への印刷で網点を用いることは殆どなく、またFMと称してはいるが使っているのはGIMPのディザ拡散の機能を利用している。
*2:少々分かりずらいかもしれないので、図で説明するとこんな感じ;

FM網点の様子
*3:メジューム、ハーフトーンベース、KSなどと名称を記したが、実はインクメーカーによって呼び名が違う。名前は違っても同じ効能を持つインクはそれぞれのインクメーカーで用意されており、どのメーカーのものが良いかは、一概には言えない。
*4:無論工業品印刷の場では許されない。それだけに印刷しながら(自分の好みで!気分で!勝手に!)色を変えていくというダイナミックな行為は ”非常に” 気持ちが良い。
*5:スキージーとは(ご存知の方も多いと思われるが)スクリーンの上のインクを押し出すゴムべらのような道具である。この道具の扱い次第でインクの出る量などコントロールし、精細な印刷結果に繋げる。概要的にはインクを版から「押し出す力(結果として版から吐出されるインク量)」は、スキージーと版面との接触角度によって変化し、角度が低い(「寝かせる」)と押し出す力が強く、角度を高くすると(「立てる」)力を抑制する方向に働く。この角度が最終的にどのように決定されるかは「印刷された結果、および人の経験と勘」と言えばそれまでだが、この結果に関わるスキージーの角度以外のパラメーターだけでも、スキージーの硬度/スキージーエッジの状態/スキージー摺動条件(圧力/スピード)があり、そしてスキージー以外の要素としては...(中略)...等々が相互にバランスが取れた状態で初めて良い印刷結果となるため、分析すれば力学的にベストな均衡点を導くことも不可能ではないように思えるが、そこまでする話でも無いためかあるいは需要がないのか、自動でグッドポイントを割り出して印刷できるようなマシンは聞いたことがない。この辺の話が大変イメージしやすく説明されているサイトがあったのでリンクさせていただく。
*6:結局「好み」と言えばいい加減過ぎるが、一応メーカー推奨の基本配合比というものがある(ちなみに800メジューム[75]:パール顔料[25])のだが、この比率だと若干パール顔料の持つマイカ色が出過ぎる(=ややベージュがかった色)ように感じるので、これより顔料比率を落として使用している。

シルク2工程目:パールまで印刷了